How to Recognize What is Porosity in Welding and Improve Your Technique
Wiki Article
The Science Behind Porosity: A Comprehensive Guide for Welders and Fabricators
Comprehending the detailed systems behind porosity in welding is essential for welders and producers making every effort for flawless craftsmanship. From the structure of the base products to the ins and outs of the welding process itself, a wide range of variables conspire to either aggravate or alleviate the visibility of porosity.Comprehending Porosity in Welding
FIRST SENTENCE:
Exam of porosity in welding reveals essential understandings into the stability and top quality of the weld joint. Porosity, characterized by the existence of cavities or voids within the weld steel, is an usual concern in welding procedures. These voids, otherwise correctly addressed, can endanger the structural integrity and mechanical properties of the weld, leading to prospective failures in the ended up item.
To find and quantify porosity, non-destructive screening approaches such as ultrasonic testing or X-ray assessment are often used. These strategies permit the recognition of inner problems without compromising the integrity of the weld. By assessing the dimension, shape, and circulation of porosity within a weld, welders can make informed decisions to enhance their welding procedures and accomplish sounder weld joints.
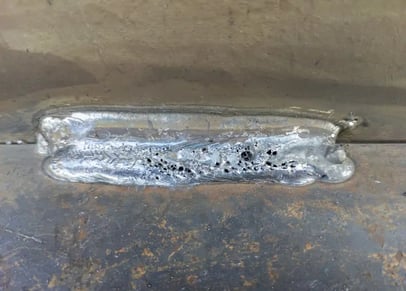
Variables Influencing Porosity Formation
The event of porosity in welding is influenced by a myriad of variables, ranging from gas securing effectiveness to the complexities of welding specification setups. Welding parameters, including voltage, existing, take a trip speed, and electrode type, also influence porosity development. The welding method utilized, such as gas steel arc welding (GMAW) or protected metal arc welding (SMAW), can affect porosity formation due to variations in warmth distribution and gas protection - What is Porosity.Effects of Porosity on Weld Top Quality
The presence of porosity additionally weakens the weld's resistance to rust, as the caught air or gases within the gaps can respond with the surrounding environment, leading to deterioration over time. Furthermore, porosity can prevent the weld's capacity to endure pressure or impact, additional jeopardizing the overall quality and dependability of the welded structure. In vital applications such as aerospace, automotive, or structural building and constructions, where security and resilience are vital, the damaging effects of porosity on weld quality can have serious consequences, try this website highlighting the relevance of reducing porosity with proper welding methods and treatments.Methods to Lessen Porosity
In addition, making use of the ideal welding parameters, such as the appropriate voltage, current, and travel speed, is important in protecting against porosity. Preserving a consistent arc size and angle throughout welding also helps reduce the chance of porosity.
Utilizing the appropriate welding technique, such as back-stepping or using a weaving motion, can also aid disperse warmth evenly and reduce the opportunities of porosity formation. By implementing these methods, welders can successfully decrease porosity and produce high-quality bonded joints.
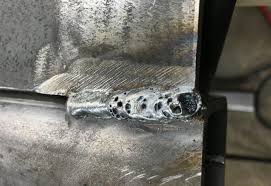
Advanced Solutions for Porosity Control
Applying advanced innovations and innovative techniques plays a crucial role in accomplishing superior control over porosity in welding procedures. One sophisticated solution is the use of advanced gas combinations. Protecting gases like helium or a combination of argon and hydrogen can assist lower porosity by providing much better arc stability and enhanced gas coverage. Additionally, employing advanced welding strategies such as pulsed MIG welding or customized ambience welding can likewise assist alleviate porosity issues.An additional sophisticated remedy entails making use of innovative welding devices. Making use of devices with built-in features like waveform control and innovative power resources can Read More Here improve weld top quality and minimize porosity threats. Additionally, the implementation of automated welding systems with specific control over specifications can dramatically reduce porosity issues.
Additionally, incorporating innovative monitoring and examination modern technologies such as real-time X-ray imaging or automated ultrasonic screening can assist in finding porosity early in the welding process, permitting immediate corrective activities. On the whole, integrating these advanced options can substantially boost porosity control and enhance the overall high quality of welded components.
Conclusion
In verdict, comprehending the scientific research behind porosity in welding is essential for welders and makers to produce top notch welds - What is Porosity. Advanced remedies for porosity control my sources can better enhance the welding procedure and make sure a solid and reputable weld.Report this wiki page